The Forged Billet Dynalite-M is further enhancement of the venerable Forged Dynalite series calipers. Specifically designed to enhance outboard clearance and is the basis for Wilwood’s new Classic Style brake kits. The latest applied developments and innovations in caliper design and manufacturing processes have resulted in substantial improvements in strength and performance over all comparable models.
The Forged Dynalite-M is the strongest calipers in the class, with weights starting at 2.80 pounds. The process of stress-flow forging re-aligns the metal's grain structure within the contour of the caliper body. This process eliminates the breaks and interruptions to the internal grain structure that occur when machining a straight block billet. The FEA generated radial transition design eliminates steps and shoulders in the area between the piston housing body and the caliper bridges. Incorporating a radius in this transition area substantially increases resistance to deflection and caliper separation under load. Structural deflection and volume displacement tests have proven the Forged Dynalite to outperform all existing styles of this popular caliper size. Without even considering the overall greater strength and reliability of the forging, the reduced deflection tendencies and the resulting decrease in fluid volume displacement translate to increased clamping efficiency with less pedal travel. The bottom line is a taller pedal and better stopping power.
The superior strength of this innovative design is combined with proven performance features from Wilwood's earlier designs. Each caliper is equipped with Wilwood's SRS stainless steel bridge plates. The SRS plates eliminate the bridge wear caused by pad gouging and extend the service life of the caliper body. The spring-loading action of the SRS plates also eliminates pad rattle and dampens the vibration harmonics that contribute to squeal under braking. Other standard Wilwood features include high temperature seals and stainless steel pistons to eliminate corrosion and retard heat transfer from the pads. Internal fluid passages eliminate the need for external tubes. Four corner bleed screws assure simple and effective air evacuation from the system and allow one caliper to be mounted in any front, rear, right or left position. Standard race calipers feature Wilwood's signature bright black anodized finish to resist corrosion and maintain their high tech style
About Wilwood Engineering
Wilwood Engineering designs and manufactures high-performance disc brake systems. Since the company’s inception in 1977 by Bill Wood, we have developed a substantial matrix of brake components and engineering techniques that allow us to quickly and reliably create brake systems for almost any application. Our core ability is the rapid development of custom engineered brake systems using a combination of off-the-shelf and custom components. In addition to designing and manufacturing brakes for all types of competitive motor sports, Wilwood also manufactures brake systems and components for agricultural equipment, industrial applications, utility vehicles, snowmobiles, quads, motorcycles and military vehicles.
With headquarters in Camarillo, California, Wilwood employs approximately 250 people. We have on-shelf stock of more than 300 different brake calipers, 200 rotor designs, 100 master cylinder designs and a wide assortment of brackets, fittings, valves and brake lines. Our off-shelf brake calipers range in size from tiny calipers used on go-carts and light duty industrial equipment, to heavy duty original equipment brakes for the U.S. military Humvee.
Wilwood's engineering department uses the latest computer-aided design and manufacturing techniques in conjunction with finite element analysis, dynamic test and cycle test equipment, to find high-performance and reliability solutions for the most difficult braking tasks. Our extensive inventory of proprietary on-the-shelf components allow us to provide cost-effective solutions for unique brake applications.
Wilwood is ISO 9000 compliant and has extensive experience maintaining quality levels of 100ppm or less for original equipment manufacturers.
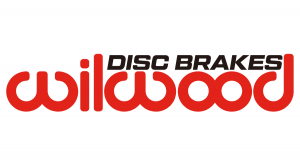